Aileron Hinge Brackets
The outboard aileron hinge brackets are aluminum and have been virtually trouble free with the exception of failure due to damage from external impact.
The inboard hinge brackets however suffer several design flaws. First of all, they are a magnesium forging which is highly susceptible to corrosion. When they corrode not only does some of the structure “disappear” but each pit is a potential crack. Secondly, the problem is enhanced by the dissimilar metal contacts between the bracket and the rear spar, bearing and mounting hardware. Last of all, the bearings were pressed in with an interference fit thus “pre-stressing” the entire bearing boss area of the forging.
These features have resulted in cracking problems in the bearing boss and in the four drilled mounting pads. Beware, paint can conceal critically dangerous cracking! If I had to choose only one component to inspect on the 190/195 prior to flying, it would be a tie between these brackets and fuel quantity.
We have re-designed these brackets using 2024 aluminum with increased cross-sectional area where possible. The new design is vastly improved in the areas listed above and is much stronger than the original unit was when new.
After bead blasting several sets of brackets for inspection, I am realizing that this problem is more severe than we thought. Of the hundreds we have examined/replaced 100% are corroded, 70% badly corroded, and 30% are cracked. Many of these cracks were concealed by the paint. The scary part of all of this is that most of these brackets looked very good until bead blasting which revealed a black corrosion by-product concealed and held in place by the high quality urethane paints usually used on aircraft. I urge everyone to have these brackets removed and bead blasted (with fresh glass bead so as not to impregnate the magnesium with a dissimilar metal) to see what really exists beneath that nice looking coating of paint. The AD does not state this but any other means will not be effective in removing the corrosion by-products (salts) from the deep pits they have created.
* BREAK TEST *
In November of 2000 we conducted a test using an inboard aileron hinge bracket that was cracked across the aft portion of the bearing boss. With the ailerons locked in the trailed position a vertical force was applied to the trailing edge of the aileron with the cracked bracket. 43 pounds of force broke the bracket which would leave the inboard end of the aileron attached by its control rod with potentially high air loads pulling at it. Without a wind tunnel I cannot say for sure what would happen from that point on, however, my opinion is that the best one could hope for is the aileron to depart the aircraft completely.
UPDATE – MAY 2004
CESSNA MANDATORY SERVICE BULLETIN – SEB04-1
Cessna has issued a Mandatory Service Bulletin requiring the removal and inspection of both inboard aileron hinge brackets at every annual inspection. This applies to the magnesium brackets only and does not apply to our aluminum bracket kits.
WARNING: The service bulletin (SEB04-1) states that the Magnesium brackets have a -477 number on them. We have not found this number on any of the original Magnesium brackets. We do however find a casting number of 0322707-2 on them. If you have any doubt as to the material of your brackets we will be glad to help you in this determination.
Cessna has some replacement brackets made from aluminum. They are priced at $2532.00 for the pair. They need to be primed and painted and do not come with installation hardware (we assume the bearings are installed as there is no mention of this). Our STC/PMA set sells for about half of that and are ready to install, painted (grey urethane) and include new upgraded installation hardware. We have made every effort to keep the cost of our kit down while keeping quality at the highest levels.
AD 04-21-08
The FAA has issued this AD requiring the inspection /replacement of the Inboard Aileron Hinge Brackets. the instructions in this AD do not require the removal of paint by bead blasting but rather by chemical means. This is NOT acceptable for the inspection of these Magnesium brackets. The main issue with this is the fact that Magnesium corrosion salts are equal in volume to the parent metal and paint stripper will NOT remove them. The only way to identify them after chemical stripping is by their slightly darker color which is almost impossible to see. Even if they could be identified, there is no way of determining how deep they run. The AD instructions also allow the situation where the highly corrosive agents in the stripper are exposed to this HIGHLY reactive metal. They will get into any pits, cracks, and in between the bearing and boss. This will make the situation much worse. We can not say not to follow the FAA instructions. What we can do is state facts and remind everyone this is a very serious issue with regards to their safety.
See pictures below of typical pitting and cracking of original style brackets as well as pictures of replacement brackets.
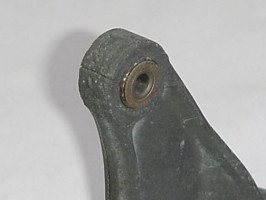